Fume Extraction Standards & Regulations: The Essential Guide to Safer Workspaces and Smarter Investments
Global market changes Day by day, manufacturers and companies need to comply with standards and regulations at every manufacturing process, such as welding, brazing, oil mist, dust collection, laser marking, laser cutting, etc. These processes need to comply with the safety standards and government regulations for each process as per the latest government norms specified.
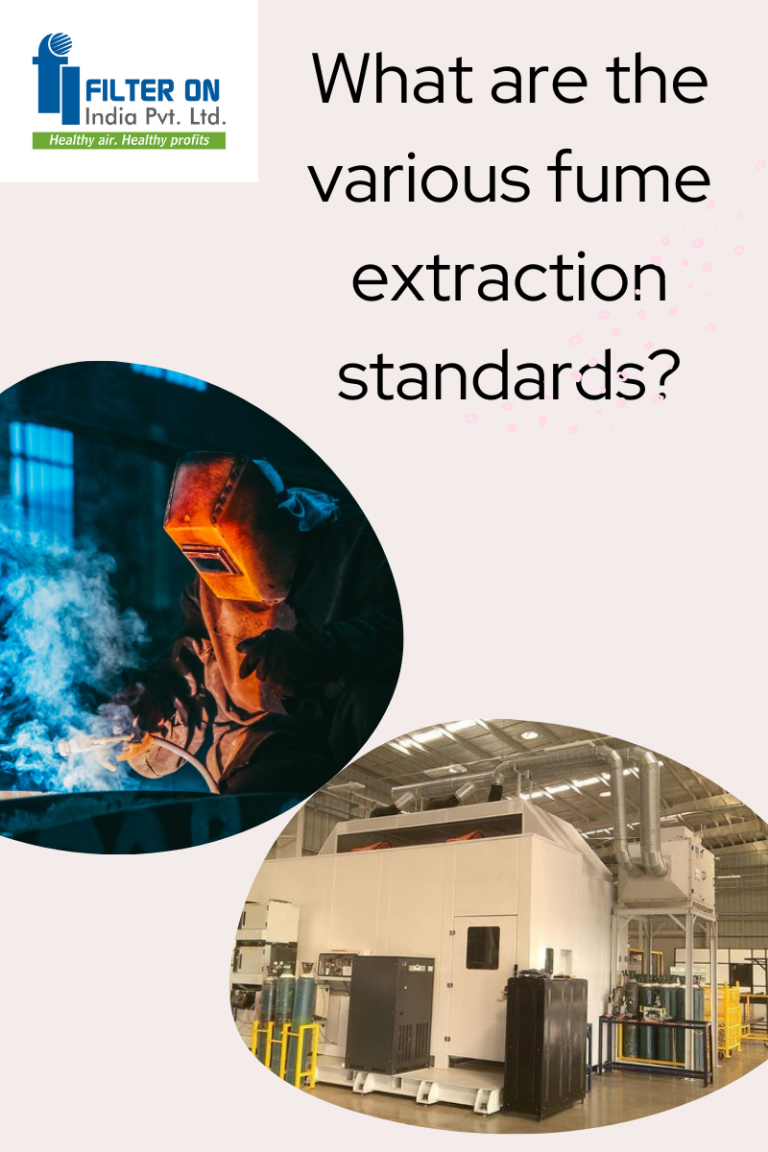
Safety Standards and Exposure Limits For Workers—Welding Applications:
As per the OSHA factsheet and India's PEL (Permissible Exposure Limits), the welding process is as follows:
OSHA standards for galvanized steel:
OSHA warns of welding hazards in galvanized steel and stainless steel. Galvanized steel, coated with zinc, can cause metal fume fever.
Want to know about health hazards related to welding fumes? Click here to read more.
OSHA standards for stainless steel:
Stainless steel coated with chromium is highly toxic and can cause cancer. Companies have a duty to guarantee that no worker is exposed to levels of chromium greater than 5 µg/m³.
The Indian government's Factory Act also follows these standards to control oil and coolant mist exposures in India. Vent lines at lubrication points are also required to collect stray mist.
Safety Standards and Exposure Limit for Workers: Laser Marking Applications:
- The Occupational Safety and Health Administration (OSHA) has established safety limits for laser marking, categorized into different classes based on their power and potential hazards.
- Class 1 is safe under all conditions, while Class 2 is safe for short viewing times but can cause eye damage if mishandled.
- Class 3B is unsafe for direct viewing and can cause skin and eye injuries.
- Class 4 is high-power lasers that can cause skin and eye injuries and fire hazards.
- Laser beams should not be directed at employees, and systems should not be operated in rainy, snowy, or dusty weather conditions.
- Other safety limits include limiting diffused reflected light to 2.5 watts per square centimeter, preventing employees from exposure to microwave power densities above 10 milliwatts per square centimeter, and having removable panels and doors with interlocks that automatically reduce or stop laser emissions when the enclosure is opened.
Safety Standards and Exposure Limit for Workers: Laser Cutting Applications:
- The Occupational Safety and Health Administration (OSHA) has established safety limits for laser equipment, categorized by power and hazard level.
- Class III B lasers are moderate power, while Class IV high power lasers pose hazards to view, ignite materials, and produce air pollutants.
- It is not appropriate to point the laser beam toward workers, and it is not advisable to run systems in wet, snowy, or dusty environments.Laser equipment labeling should indicate its maximum output, and Class IIIB or Class IV lasers should be enclosed in a Class I enclosure or have a Laser Safety Officer present.
- Ideally, the laser unit should be set up above employees' heads.
Visit blogs to learn more about the critical features of clean air system design and air pollution control systems created by Filter On India.
Filter On India has been working towards “Mission Zero Pollution” for the last 40+ years as a clean air solutions partner for industries. We specialize and have expertise in welding fumes, oil mist, coolant mist, dust collection, soldering, laser marking, laser cutting, plasma cutting, fumes in fastener manufacturing, ball point tip manufacturing, oil quenching, kitchen fumes, etc. Filter On has 70+ clean air solutions, so you can contact us for more information about our solutions. You can reach us through the web or visit us at our corporate office at Pune and our virtual locations at Delhi, Bangalore, Ahmadabad, Hyderabad, or Chennai locations.
Facebook
Twitter
LinkedIn