Workplace Air Quality Monitoring: A Vital Tool for Enhancing Health and Productivity
- filterontest
- March 21, 2025
- 10:55 am
- No Comments
Workplace air quality worsens day by day. In the previous blog, we discussed how important air quality mapping is for your workplace air quality improvement. In this blog, we are going to discuss how to measure air quality in the workplace and workplace air quality monitoring using a live case study example.
One of the world's most well-known vehicle chassis manufacturers is experiencing poor air quality at their welding section, so they contacted us to investigate the cause. We have planned a systematic approach to solve this particular case. We plan the following steps:
- We conducted an air quality mapping test to learn about fume exposure at the workplace.
- Based on the outcomes of the first test, we implemented the solutions in a phase-wise manner for each welding station.
- We conducted the second test after two months of implementation of solutions to test the effectiveness of fume extraction solutions.
- The analysis uses a live comparison to get precise conclusions.
Please check the below summary to understand the overall case.
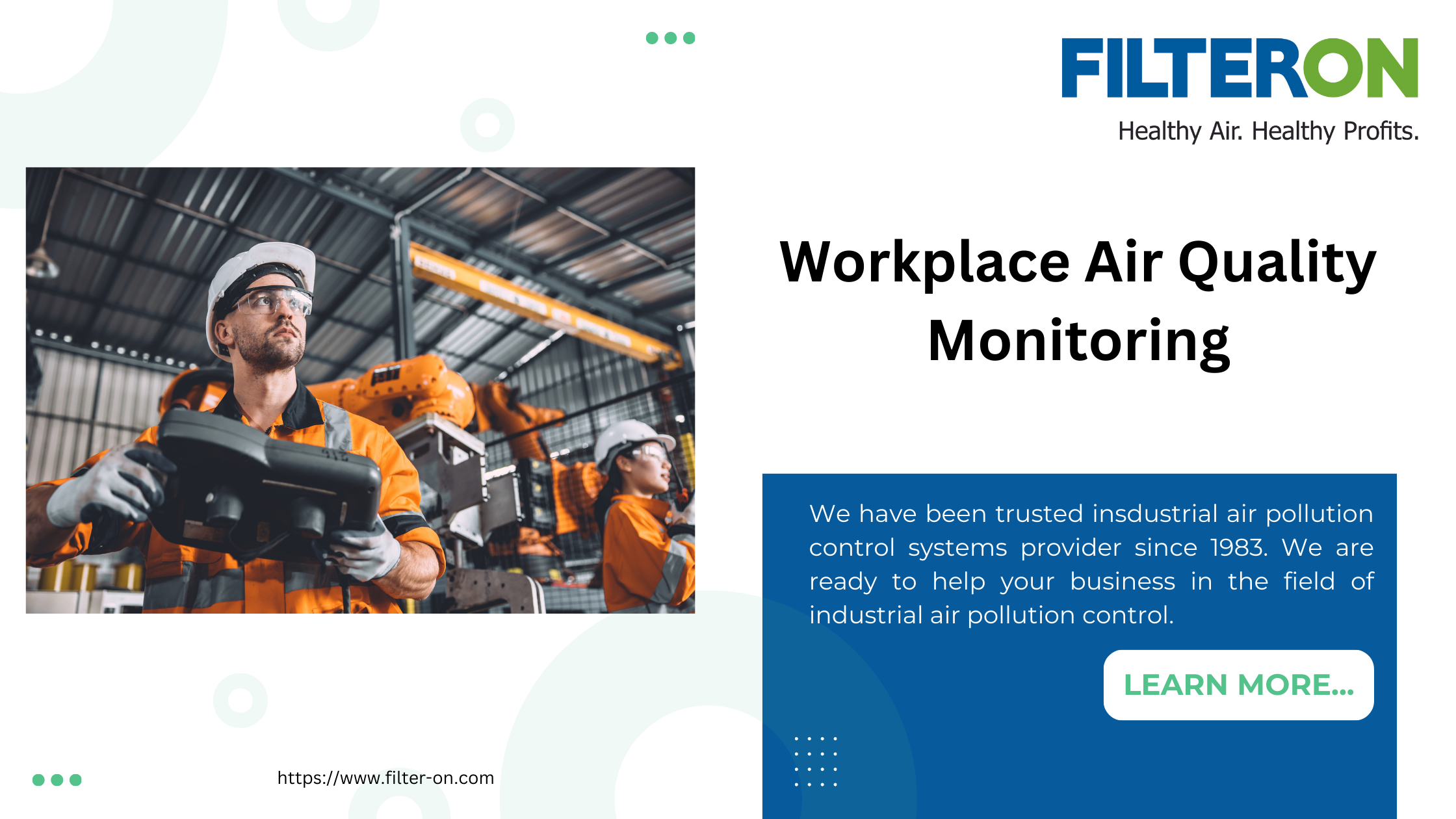
Summary of the case: How to measure air quality.
An internationally renowned auto chassis manufacturer has experienced problems with air quality at its Pune, Maharashtra, India, plant.
As a first step, the FILTER ON team decided to conduct air quality mapping of the work area.
Problems Faced By Client:
- They want a clear understanding of the status of the workplace air quality..
- They want to check the effectiveness of analyses after the implementation of solutions at their welding stations.
- They face fume exposure around the workplace due to the unavailability of fume extraction systems.
.
- Workers face serious health concerns and productivity loss due to fume exposure at the workplace.
Actual Test & Results
We have carried out a workplace air quality mapping test in the six welding stations (W-3029, W-3012, W-3019, W-3047, W-3056, and W-3040). We tested the fumes' exposure to a variety of contaminants, including PM, CO, CO₂, SO₂, and O₂. The results were calculated throughout a 30-minute test period. The result was the outcome of a 30-minute test period. These results revealed that total particles were on the borderline at some locations when compared to permitted limits, while other measures, while still below permissible limits, were on the higher side, causing irritation and health risks for the operators.
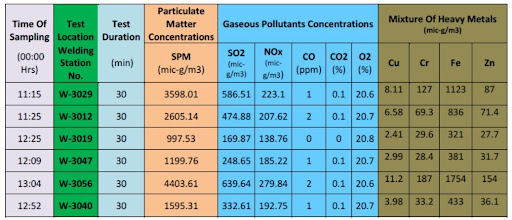
Fig. 1: Status of results before implementation of fume extraction systems
Solutions & Approach for Fume Extraction System Implementation:
After analyzing the workplace air quality data in Fig. 1 and the actual working conditions at the plant site, we designed a comprehensive strategy for minimizing fume exposure that utilized our best technology, electrostatic precipitation, to efficiently capture and filter the fumes. We implemented a solution with a fume extraction system with filtration units that included a canopy, hoods, ducting, filtration, and blower motor assembly as per suction parameters for each welding station.
This implementation provides clean air in the workplace, along with the following:
- Lower pressure drop
- Saves space on the shop floor
- Duct lengths optimized
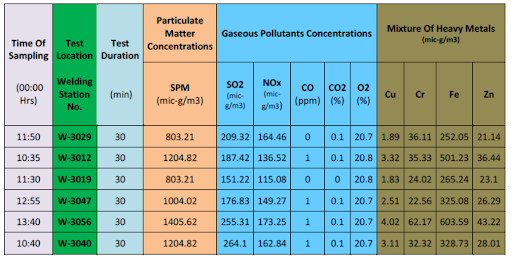
The following are the outcomes of the mapping test for workplace air quality: The following image shows a comparison of both test results.
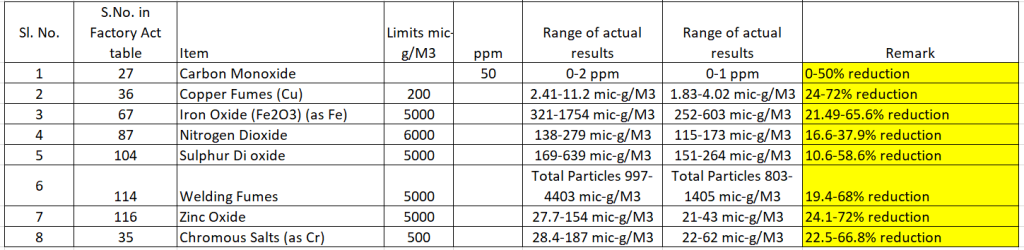
Key takeaways from the workplace air quality mapping test:
The key takeaways from the results are as follows:
- We assessed the pollutants such as CO, Cu, Fe, NO₂, SO₂, CO₂, welding fumes, zinc oxide, and Cr.
- We measure each pollutant's permissible limits adhered to the Indian Factory Act.
- There is a reduction percentage of 10% to 72% for the various pollutants after the implementation of the Fumes Extraction System.
Welding fumes decreased by about 68% as compared to the previous state.
- We found that there is the least reduction in sulfur dioxide and nitrogen dioxide, whereas copper fumes and zinc oxide show the highest reduction.
- After implementing the solution, we can say that there was a significant reduction in fume exposure, and the workplace is now much safer and healthier than before, and thus more productive too!
- Due to the air quality mapping exercise, it was easier to design optimum systems and also assess the performance of the system in very objective terms.
- Also, this data was useful to the client for regulatory compliance required under EMS/OSHA/Factory Act, etc.
To know more about fume extraction standards and regulations, please check here.
Visit blogs to learn more about the critical features of clean air system design and air pollution control systems created by Filter On India.
Filter On India has been working towards “Mission Zero Pollution” for the last 40+ years as a clean air solutions partner for industries. We specialize and have expertise in welding fumes, oil mist, coolant mist, dust collection, soldering, laser marking, laser cutting, plasma cutting, fumes in fastener manufacturing, ball point tip manufacturing, oil quenching, kitchen fumes, etc. Filter On has 70+ clean air solutions, so you can contact us for more information about our solutions. You can reach us through the web or visit us at our corporate office at Pune and our virtual locations at Delhi, Bangalore, Ahmadabad, Hyderabad, or Chennai locations.
Facebook
Twitter
LinkedIn